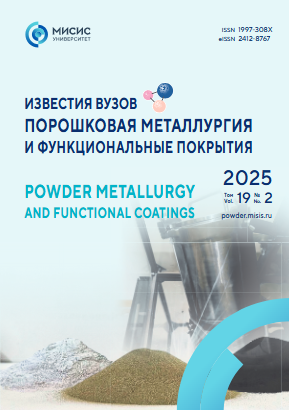
Научное периодическое издание «Известия вузов. Порошковая металлургия и функциональные покрытия» было создано в 2007 г. по инициативе научной общественности как единственный в России журнал по специальности «Порошковая металлургия и композиционные материалы».
В его редакционную коллегию входят ведущие ученые в области порошковой металлургии, инженерии поверхности, наноматериалов и нанотехнологий . Журнал ориентирован на широкий круг читателей (металлургов, материаловедов, физиков, химиков) и публикует научные статьи работников вузов, РАН, отраслевых институтов и компаний России, стран СНГ, зарубежных авторов, посвященные следующим аспектам теории и научно-обоснованной практики в области порошковой металлургии и инженерии поверхности:
– Процессы получения и свойства порошков;
– Теория и процессы формования и спекания порошковых материалов;
– Самораспространяющийся высокотемпературный синтез (СВС);
– Тугоплавкие, керамические и композиционные материалы;
– Пористые материалы и биоматериалы;
– Материалы и покрытия, получаемые методами аддитивных технологий;
– Модифицирование поверхности, в том числе пучками заряженных частиц, потоками фотонов и плазмы;
– Наноструктурированные материалы и функциональные покрытия;
– Применение порошковых материалов и функциональных покрытий.
Значительный объем публикуемых в журнале статей относится к критическим технологиям (нанотехнологии и наноматериалы, технологии создания и обработки композиционных и керамических материалов, технологии создания биосовместимых материалов) приоритетного направления «Индустрия наносистем и материалы».
Журнал входит в Перечень рецензируемых научных изданий (Перечень ВАК), в которых должны быть опубликованы основные научные результаты диссертаций на соискание ученой степени кандидата или доктора наук по научным специальностям:
- 2.6.5. Порошковая металлургия и композиционные материалы (технические науки)
- 2.6.6. Нанотехнологии и наноматериалы (технические науки)
Журналу «Известия вузов. Порошковая металлургия и функциональные покрытия» присвоена категория К1 в соответствии с методикой, разработанной ВАК Минобрнауки (письмо от 06.12.2022г. № 02-1198) на основе анализа Перечня рецензируемых научных изданий https://vak.minobrnauki.gov.ru/uploader/loader?type=19&name=92263438002&f=14239 (№ 1017).
По базе глобального цитирования «Scopus»: CiteScore2022 – 0.3 и SJR2022 – 0.113; Q4
Подписка на журнал в печатной и электронной формах осуществляется через агентство "Урал-Пресс" http://www.ural-press.ru/
С 2013 г. опубликованным в журнале статьям присваивается DOI.
Журнал индексируется в различных базах данных. Журнал включен в базы данных SCOPUS и Russian Science Citation Index на платформе Web of Science"
Текущий выпуск
Процессы получения и свойства порошков
Представлены результаты проведенных в Институте порошковой металлургии имени академика О.В. Романа (Беларусь) работ по изучению процессов получения псевдосплавов антифрикционного назначения с каркасом на основе железа и разработке способов повышения их механических и триботехнических свойств. Создана расчетная модель параметрически нестационарной высокотемпературной инфильтрации, позволившая рассчитать время заполнения пор и оптимизировать режим получения псевдосплавов. Выявлены особенности распределения углерода в стальном каркасе псевдосплава при изотермической выдержке и термической обработке из-за воздействии медной фазы. Показано, что после изотермической выдержки содержание углерода в приграничной с медной фазой области стального каркаса меньше, чем в центре, а после закалки и высокотемпературного отпуска на границе с медной фазой образуется область с повышенным содержанием углерода. Установлены механизмы, обеспечивающие повышение механических и триботехнических свойств псевдосплавов на основе железа с помощью разработанных способов: штамповкой при оптимальной температуре; увеличением выдержки при высокотемпературном отпуске после закалки; высоко- и низкотемпературной термомеханической обработкой при оптимальных режимах; легированием стального каркаса никелем или хромом; модифицированием структуры введением ультрадисперсных алмазов, ультрадисперсного оксида алюминия, нанодисперсного оксида циркония, смеси наноразмерных оксидов железа, никеля и цинка, а также алюминидов никеля, железа, титана (однофазных или двухфазных) и композитов на их основе, молибдата кальция или гексагонального нитрида бора; легированием инфильтрата оловом, никелем, хромом и введением в него ультрадисперсного оксида алюминия. Приведены достигнутые значения прочности, твердости, ударной вязкости, коэффициента трения, предельного давления схватывания, износостойкости, параметра PV. Установлен механизм изнашивания псевдосплавов с повышенными свойствами. Показано, что в процессе трения происходит образование наноразмерной пористости и лакун, являющихся дополнительными резервуарами для смазки, что улучшает условия трения, препятствует переносу в эти места меди, обеспечивает снижение коэффициента трения и повышения износостойкости.
Теория и процессы формования и спекания порошковых материалов
Работы в области порошковой металлургии титана проводятся уже более 60 лет. Несмотря на это, примеров практического использования порошкового титана не так много, что связано с неудовлетворительным характером показателей надежности и долговечности получаемых изделий. Способность титановых изделий сопротивляться воздействию статических и динамических нагрузок определяется наличием остаточной пористости, неметаллических включений, а также характеристиками микроструктуры. В настоящее время при изготовлении изделий из порошкового титана наибольшее распространение получила технология прессования–спекания. Однако пористость спеченного титана составляет 3–15 %, что снижает его сопротивляемость действию нагрузок и обусловливает актуальность разработки эффективных методов снижения пористости. Большой потенциал в решении указанной задачи имеют методы горячей обработки давлением, в частности горячая штамповка пористых заготовок. В работе представлены результаты исследования особенностей уплотнения, формирования структуры и свойств порошкового титана при горячей штамповке. Предложена технология получения горячештампованного порошкового титана, включающая выполнение операций гидрирования–дегидрирования пористой заготовки, обеспечивающих восстановление оксидов, локализованных на поверхностях открытых пор, водородом и их активизацию, что способствует улучшению условий формирования межчастичного сращивания при последующей горячей допрессовке и повышению трещиностойкости и пластичности получаемых образцов в сравнении с образцами-свидетелями. Установлены значения величины максимальной приведенной работы горячего уплотнения пористого порошкового титана, необходимой для достижения плотности монолита, при разных температурах преддеформационного нагрева заготовок. Показано, что немонотонность температурной зависимости максимальной приведенной работы уплотнения связана с формированием крупнозернистой структуры и с уменьшением пластичности деформируемого материала в интервале температур фазового α → β-превращения.
Самораспространяющийся высокотемпературный синтез
Методом самораспространяющегося высокотемпературного синтеза (СВС) в режиме теплового взрыва получен карбид Ta4ZrC5 . Изучен механизм его формирования, включающий процессы в ходе нагрева смесей прекурсоров до температуры воспламенения, протекающие в твердой фазе. Исследовано взаимодействие расплавленных биметаллических частиц состава Ta4Zr с углеродом. Исходные смеси порошков готовили в две стадии. На первой – методом высокоэнергетической механической обработки (ВЭМО) в активаторе АГО-2 в атмосфере аргона происходило механическое сплавление (МС) смеси тантала с цирконием и формировались биметаллические частицы состава Ta4Zr, представляющие собой твердый раствор циркония в тантале. При их нагреве происходило упорядочение твердого раствора и наблюдалось небольшое тепловыделение, зависящее от времени МС. На второй стадии полученный порошок Ta4Zr смешивали с сажей и нагревали до температуры теплового взрыва (900–1250 °C), в результате которого образовывалось соединение Ta4ZrC5 . Впервые для исследования механизма высокотемпературного взаимодействия биметаллических частиц Ta4Zr с углеродом их наносили на подложку из графита и нагревали в вакууме при остаточном давлении 10–3 Па и температуре подложки до 3000 °C. В зависимости от размера частиц наблюдались два режима взаимодействия расплавленных частиц Ta4Zr с подложкой из графита. Частицы размером менее 10 мкм из-за сил поверхностного натяжения при плавлении не растекались по подложке, а, растворяя в себе углерод, в нее погружались. Частицы большего размера растекались по подложке, причем расплав обеднялся цирконием, который более активно взаимодействовал с углеродом.
Тугоплавкие, керамические и композиционные материалы
Коррозия теплозащитных покрытий деталей газотурбинных двигателей, выполненных из жаропрочных сплавов, обусловленная взаимодействием с расплавленными силикатными отложениями (CMAS), снижает их устойчивость к высоким температурам и приводит к преждевременным отказам в эксплуатации. Проблема стойкости к CMAS покрытий с внешним керамическим слоем из диоксида циркония, стабилизированного иттрием, остается весьма актуальной, и ее решение имеет важное практическое применение. Объектом изучения в настоящей работе являлись керамические материалы на основе диоксида циркония, используемые для нанесения теплозащитных покрытий. Исследовано взаимодействие керамических покрытий с силикатными отложениями при температурах до 1300 °С. С помощью сканирующей электронной микроскопии, энергодисперсионной спектроскопии, дериватографии и рентгеноструктурного анализа выполнены исследования взаимодействия CMAS с керамикой YSZ на модельных образцах из порошков марок Z7Y10-80A, Zr7Y20-60 и Metco 204NS различной морфологии. Установлен механизм взаимодействия CMAS и YSZ при t = 1200÷1300 °С. Показано, что характер и интенсивность взаимодействия существенно зависят от строения и морфологии частиц керамики. Плотная структура частиц керамики на основе порошков Z7Y10-80A и Metco 204NS снижает проникновение CMAS в отличие от Zr7Y20-60 с более пористой структурой частиц. Установлено, что характер взаимодействия между CMAS и YSZ един для всех исследуемых керамик и происходит по механизму растворения–осаждения оксида циркония в расплаве стекла. Показано, что с ростом температуры происходит изменение степени тетрагональности оксида циркония, обусловленное снижением содержания иттрия из-за его диффузии в стекло. Это может привести к полиморфной трансформации диоксида циркония с увеличением объема, последующим растрескиванием и отслоением теплозащитного покрытия.
Наноструктурированные материалы и функциональные покрытия
Изучены закономерности формирования стойких к износу и окислению покрытий при комбинированной электроискровой и катодно-дуговой обработке (ЭИКДО) жаропрочного сплава АЖК. Исследовано влияние полярности стержневых электродов на основе Al–Ca и их микролегирования РЗМ (Ce, Er) на структуру, упрочнение и жаростойкость полученных покрытий. Установлено, что при подключении электрода с анодной полярностью формируются покрытия без трещин на основе интерметаллида γ′-Ni3Al (тип L12 , 3,600 Å). Их толщина достигает 15–20 мкм в результате направленного роста кристаллитов с поперечным размером менее 300 нм. При подключении к электроду катодной полярности формируются покрытия, в структуре которых найдены зерна двух интерметаллидов: β-NiAl (тип B2, 2,895 Å) и γ′-Ni3Al (тип L12 , 3,595 Å). Структурно-фазовые превращения, происходящие при обработке электродами с разной полярностью подложки из АЖК с твердостью 5,2 ГПа, являются доминирующими факторами упрочнения. Максимальное значение твердости (12,3 ГПа) зафиксировано в покрытиях, состоящих из β-NiAl и γ′-Ni3Al. При анодной полярности электрода твердость покрытий составляет 7,3 ГПа, и при этом они имеют низкие (112 ГПа) значения модуля упругости. Величина приведенного износа покрытий находится в пределах от 6,0·10–5 до 7,5·10–5 мм3/(Н·м), что в 6 раз меньше, чем у необработанного сплава АЖК. При in-situ ПЭМ-исследовании установлена превосходная термическая стабильность интерметаллидной структуры γ′-Ni3Al при нагреве до t = 700 °C ламели, вырезанной из покрытия, полученного при анодном режиме обработки. Результаты испытаний на стойкость к высокотемпературному окислению при t = 1000 °С свидетельствуют, что покрытия меняют закон окисления сплава АЖК с линейного на логарифмический. Минимальная толщина оксидного слоя (около 3 мкм) установлена у покрытий, полученных при ЭИКДО электродом Al–Ca–Er с анодной полярностью, что в 10 раз меньше таковой для сплава АЖК. Переход к логарифмическому закону окисления обусловлен замедлением диффузии кислорода через образующийся при отжиге барьерный слой NiAl2O4/α-Al2O3 , упрочненный частицами CaMoO4 , что обеспечивает превосходную стойкость к окислению сплава АЖК.
Материалы и покрытия, получаемые методами аддитивных технологий
Представлен обзор современных достижений в области функционально-градиентного аддитивного производства по технологии селективного лазерного сплавления (СЛС). Рассмотрены основные принципы создания изделий с функционально-градиентной структурой методом СЛС, включая способы формирования градиентного состава и структуры. Описан процесс формирования переходного слоя синтезируемого материала, который является ключевым для обеспечения требуемых свойств изделий. Проанализированы методы проектирования и моделирования изделий с функционально-градиентной структурой, в том числе с использованием искусственного интеллекта и машинного обучения. Показано, что применение природоподобных принципов строения позволяет создавать изделия с улучшенными механическими, тепловыми и функциональными свойствами. Рассмотрены примеры успешного получения мультиматериальных структур с заданной анизотропией свойств, а также изделий с контролируемым градиентом пористости. Определены перспективные направления применения изделий с функционально-градиентной структурой, включая аэрокосмическую отрасль, медицину, машиностроение и энергетику.
В работе рассмотрены основные методы производства и контроля качества металлопорошковых композиций (МПК), предназначенных для применения в технологии селективного лазерного сплавления (СЛС). Метод СЛС представляет собой послойное лазерное сплавление МПК на поверхности металлической подложки в соответствии с 3D-моделью. В качестве объектов исследования использованы МПК из промышленных сплавов на основе никеля (Inconel 718, ЭП741НП, АЖК), титана (ВТ6, ВТ6с, ВТ20), железа (12Х18Н10Т, система Fe–Cr–Ni–Co–Mo) отечественного производства. Основными методами их изготовления являются газовая атомизация, плазменное центробежное распыление, плазменная атомизация в среде инертных газов. Приведены основные преимущества и недостатки каждого из представленных способов производства МПК. Рассмотрены наиболее распространенные дефекты МПК, возникающие на этапе их получения и применения в процессе СЛС, такие как несоответствие гранулометрического состава, внутренняя пористость, сателлиты, изменение насыпной плотности и текучести, нагар, увеличение содержания газовых примесей и несоответствие химического состава. Предложены основные способы их устранения для сохранения качества выпускаемой продукции. Установлено, что для получения стабильных результатов в процессе послойного синтеза методом СЛС необходимо проводить регулярный контроль качества МПК на соответствие установленным в нормативной документации требованиям (гранулометрический состав – квантили распределения d10 , d50 и d90 , технологические свойства, форма частиц, химический состав, влажность). В случае возникновения на регулярной основе дефектов, которые затруднительно и/или невозможно устранить, наилучшим решением для некоторых сплавов является смена метода производства МПК.
ISSN 2412-8767 (Online)